In 2008, China's parts and components industry still showed strong growth momentum in the face of a sharp decline in the macroeconomic downturn automobile industry. In 2008, the main business income was 948.075 billion yuan, an increase of 23.85% over 2007. The sales value of sales was 927.977 billion yuan, an increase of 24% over 2007. The proportion of parts production value to the whole vehicle also increased from 72% in 2007 to 82.6%.
The development of the parts industry is seriously behind the vehicle
Since the reform and opening up in 1978, China has gone through 30 cold summers. In the past 30 years, China's auto industry has also achieved rapid growth as a pillar industry. China has now become the world's third largest auto producer. The proportion of automobile production to world automobile production has increased year by year, from 3.6% in 2000 to around 12% in 2007. Along with the development of the whole vehicle, although the parts industry has made great progress, compared with the whole vehicle industry, the development is still lagging behind.
The lag in the development of the parts industry is mainly reflected in the backwardness of research and development capabilities, low profit levels, small scale of enterprises, and weak comprehensive strength of the industry. Compared with foreign companies, the domestic R&D investment of domestic parts companies is less than 1/4, which directly leads to the backwardness of the company's technical strength. In 2007, the average monthly profit level of the parts industry was around 7%. Compared with the production and sales links, the average profit level was the lowest. The scale of China's auto parts is generally small, and the number of parts and components enterprises above designated size accounts for less than half of the total. There are only a hundred large parts and components enterprises that can truly exceed 100 million yuan.
The strength of parts and components enterprises is seriously different
According to the data of Beijing Hongrui Xinsi Management Consulting Co., Ltd.: At present, there are more than 15,000 auto parts enterprises in China, and less than half of the total number of parts and components enterprises above the scale, and large parts enterprises that can truly exceed 100 million yuan. There are only a handful of companies, most of which are small and medium enterprises.
The development of the parts industry is double squeezed
Because of history and strength, the development of China's auto parts companies has been subject to double extrusion.
Squeeze of raw material suppliers
The primary responsibility of upstream suppliers is to use their own monopoly or oligarchic position to squeeze parts companies. For component companies, especially second- and third-tier component manufacturers (these are mainly small and medium-sized enterprises), their upstream suppliers are generally large industrial raw material enterprises. Compared with manufacturers of steel and non-ferrous metals, the bargaining power and negotiation capacity of small and medium-sized component companies are almost zero. In the face of price increases and timely delivery, component companies have no choice.
The strength of the downstream OEM
The OEM also often uses its own strong position to compress the profit margin of component companies for their own benefit. For example, when the sales decline enterprise needs to reduce the cost, the first measure adopted by the OEM is to lower the purchase price of the parts. In addition, many SMEs are responsible for the burden on the OEM.
As the cost of the near-term period rises and sales decline, the OEM is trying to reduce costs, mainly by reducing internal expenses, layoffs, and lowering the purchase price of raw materials. And low-cost acquisitions will be the most effective way to control costs. In the face of a strong OEM, most component companies do not have the ability to bargain. Therefore, the parts manufacturing enterprises are caught in the double squeeze of the upstream and downstream, and the profit margin is infinitely compressed.
According to Hongrui Xinsi Consulting, many OEMs now require third-party inventory around parts companies. The reason for the OEM is to reduce its warehouse occupancy and management costs in order to respond appropriately to market changes. Most of these third-party inventories are inextricably linked to the OEMs. This is the inventory organization, and its management is very confusing. It is not even possible to provide an inventory for companies that store parts in their warehouses. The irresponsibility of the OEM is also reflected in frequent changes to orders. The OEM can change the production orders that have been released due to changes in its production schedule and market conditions. Even some parts companies have responded to more than 30 order changes received in one month, and each has dozens of orders. Products, changes include delivery time, delivery quantity, product variety and other items. This undoubtedly increases the production cost of component companies and affects their delivery speed and quality. Frequent change orders are exposed to the lack of production management in the OEM, but this responsibility has been borne by the parts companies.
The component industry cluster effect is obvious
According to the research of Hongrui Xinsi, there are 103 major parts and components industrial parks in China. From the perspective of layout, most of these industrial parks are located in the eastern coastal areas, with Jiangsu, Hebei, Zhejiang and Fujian. Among them, there are 13 parts and components industrial parks in Jiangsu Province, ranking first in the country. Except for the five western cities in Gansu, Qinghai, Ningxia, Xinjiang and Tibet, there are no large-scale parts and industrial parks, and the rest of the provinces and cities are distributed. From the perspective of the types of enterprises, there are tens of thousands of parts and components enterprises in these parks, covering all aspects of the automobile industry chain. It can be said that the size of the cluster has been considerable. In addition, when building these industrial parks, the government has fully considered factors such as proximity and cluster advantages. The supporting relationships and complementary resources within the park have been initially reflected. For example, the Tiexi Industrial Park in Liaoning is mainly a large-scale tire enterprise, while the sputum is led by a filter, which in turn drives the rise of related industries. Although most of the individual enterprises in China's parts and components industrial parks belong to small and medium-sized enterprises, the scale is not large, but some parks have a high market share and show strong cluster advantages.
Independent parts and components enterprises are severely squeezed by foreign capital
Up to now, 70% of the top 100 auto parts suppliers in the world have come to China to conduct business, and more than 1,200 foreign-funded enterprises are engaged in auto parts production in mainland China.
In 2006, the sales revenue of the national auto parts enterprises was 403.5 billion yuan, of which foreign-funded (controlled or wholly-owned) parts accounted for most of the market share, and domestically produced parts only accounted for 20%-25%. Since the implementation of the “Administrative Measures on the Importation of Auto Parts Forming the Characteristics of Complete Vehicles†in April 2005, the enthusiasm of foreign-invested parts companies for investment in China has suddenly increased. According to statistics, there were more than 90 foreign-invested parts and components companies that signed new contracts in China, and the agreed investment amount reached 4 billion US dollars, 3.2 times that of 2004. Among them, there are many multinational giants such as Delphi, Nippon Denso, Sumitomo, American Dana, French Valeo, and Japan Fujitsu Electronics. After two years, this boom has not yet retreated.
Regional economic data analysis
Industry concentration is high, and the top ten provinces in terms of output value account for 80% of the total market. According to statistics, in 2008, the top ten provinces and cities in terms of cumulative output value were Zhejiang, Jiangsu, Guangdong, Shanghai, Shandong, Hubei, Jilin, Tianjin, Chongqing, and Henan provinces. The total output value in the first ten months accounted for 76.74% of the country. Eight of the ten provinces are located in the eastern coastal areas, while the western region only relies on Changan Automobile to drive the output value of parts in Chongqing to the top ten. This shows that the cluster of China's parts industry has taken shape.
Hongrui Xinsi suggested: “Partial development plan†for parts industry
As far as the entire auto parts industry is concerned, 90% of the market share and manufacturing capacity of China's independent parts and components enterprises are concentrated in low-end parts and components, while only 10% of enterprises are taking high-end routes and producing high technical content. The parts and components are the 10% high-end, and most of them are also joint ventures with foreign parties. If this trend is allowed to continue, China's parts and components enterprises will be completely squeezed into the low-end range, and there will never be a possibility of development. According to the research of Beijing Hongrui Xinsi, the development of the parts industry takes the path of “segmented development planningâ€, and perhaps there is still hope. Of course, the implementation of this plan requires the cooperation of all parties and needs to be long. For a while, but it can make the parts and components companies really grow up, and the price is worth it.
First of all, for 10% of high-end products, you can choose to gradually abandon the joint venture, and at the same time invest the funds and manpower extracted from the joint venture into the establishment of research institutions and university laboratories, and truly begin the road of research and development. When these high-end technologies have been localized, they will start to focus on high-end products in the parts industry and make high-end products gradually become the leading products in the parts industry. This is also a process of thick and thin hair.
For 90% of low-end products, they are divided into different stages to arrange different development directions. Some strong enterprises have begun to enter the middle-end products. This ratio may start at only 5%, but it is necessary to continuously guide and select powerful component companies to make progress and gradually expand the market share and production capacity of this region. However, there is a ceiling in the development of the mid-market, such as only 35%. Second-rate parts companies still insist on low-end products, but the company's strength should be gradually improved, and then the production of mid-end products, compress the market share of low-end products, compressed to 5% or even completely eliminated. The strength of the first- and second-rate companies is also accompanied by the acquisition and merger of third-rate companies.
The final development blueprint is that high-end products have become the leading products after thick accumulation, and the remaining market share is mid-end products, while low-end products are transferred to other underdeveloped regions and countries.
1.Automatic continuous feeding, unlimited length, improve production efficiency and reduce production costs.
2.It adopts numerical control, running information and status feedback in time, and the operation is simple.
3.The use of numerical control program adjustment ensures the machining accuracy of the workpiece.
4.Hydraulic clamping of the material, smooth operation, to ensure the processing accuracy of the workpiece.
5.The device is simple and convenient to operate, safe and reliable in performance, and high in production efficiency.
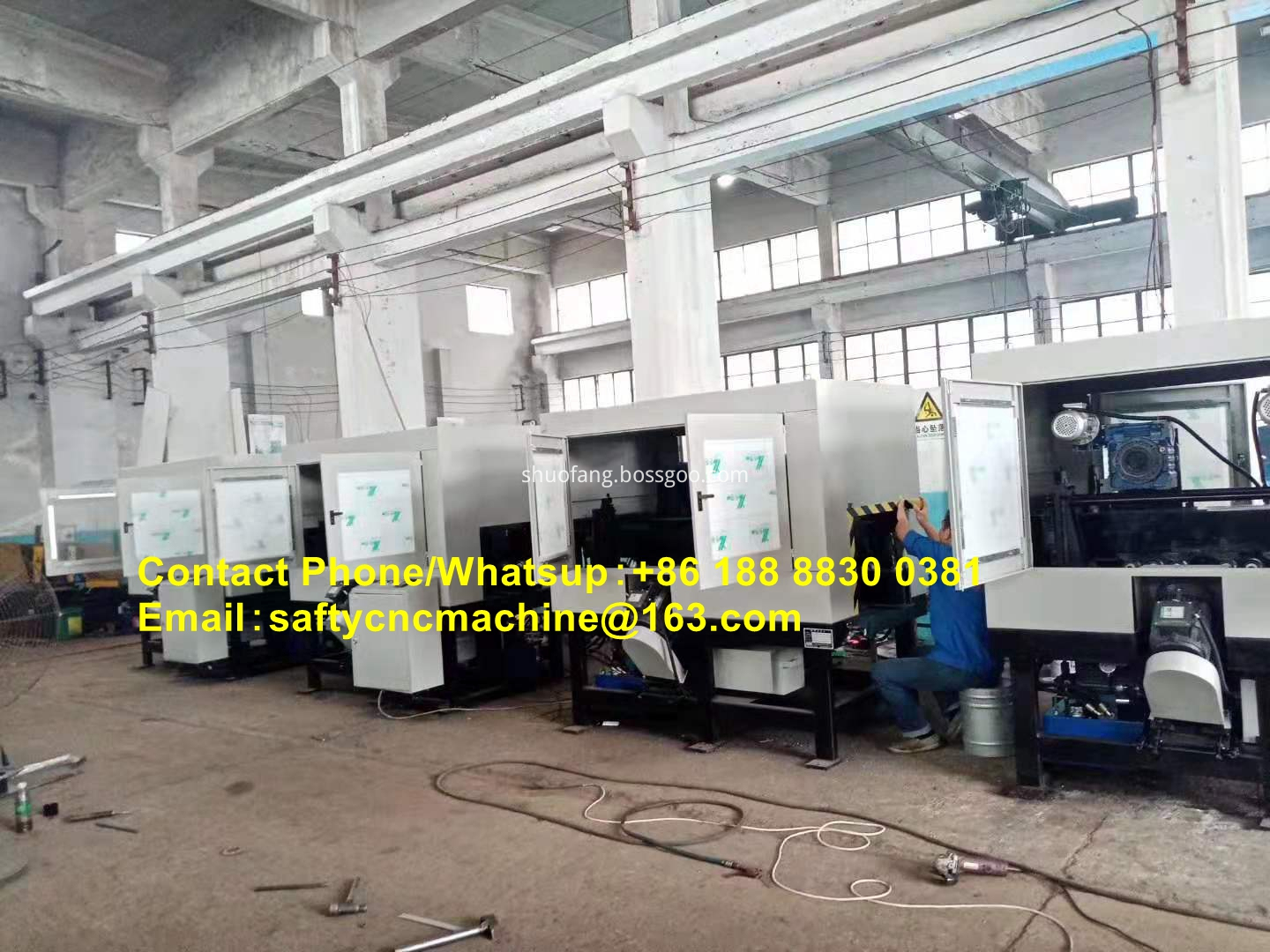
Heel Milling Machine,Milling Machine for Angle Steel Heel,Angle Steel Heel Milling,Steel Angle Milling Machine
Shandong EN FIN CNC Machinery Co., Ltd , https://www.sdfincncmachinery.com