Cubic boron nitride (CBN) is a superhard material with hardness second only to diamond. It has an oxidation temperature of up to 1 360 ° C and has excellent properties such as high hardness, high thermal stability and high chemical stability. Therefore, it is especially suitable for processing high hardness and high hardness. Tough tough metal material. Polycrystalline cubic boron nitride PCBN is a CBN sintered body for cutting tools. It is the main tool material for advanced cutting requirements. It is also an ideal tool material for hard cutting, high speed cutting and dry cutting.
1. Semi-finishing milling test of PCBN insert on the top and bottom of cylinder head
(1) Test conditions. The top surface of the cylinder head is shown in Figure 1. The main features are the intermittent surface and the lap. The cutting process is a typical interrupted cutting. The bottom surface of the cylinder head is shown in Figure 2. The main feature is that a certain number of surfaces are distributed on one surface. Hole, the cutting process is semi-continuous cutting.
Figure 1 Cylinder head top surface
Figure 2 Cylinder head bottom surface
The test tool structure is shown in Figure 3. The cutter disc has a diameter of 200 mm. There are 28 blade mounting positions on the cutter head. One of the wiper blades is installed every 90°, and the other 24 positions are equipped with cutting edges.
Figure 3 f200mm milling cutter
The cutting edge is shown in Figure 4a, the cutting edge is made of cemented carbide, and the PCBN cutting edge is bonded to the blade by brazing. The rake angle of the blade is 0°, the main declination angle is 45°, the rear corner angle is 11°, and the radial and axial rake angles are 3° to 5° after installation, and the main declination angle is 43°.
The wiper blade is shown in Figure 4b. The cutting edge is made of cemented carbide and the PCBN cutting edge is brazed to the blade. The rake angle of the blade is 0°, the main declination angle is 45°, the rear corner angle is 11°, and the radial and axial rake angles are 3° to 5° after installation, and the main declination angle is 43°.
(a) cutting edge
(b) Lightening blade
Figure 4 PCBN welding blade
Test requirements: partial flatness 0.05/100mm, surface roughness value Ra=25μm, thickness 123.5±0.05mm; test equipment: imported CNC horizontal machining center; workpiece material: HT250; workpiece hardness: 180~249HBW; cutting area: 873mm ×331mm; machining allowance 0.5mm; blade arrangement as shown in Figure 5.
Figure 5 parameters after blade installation
(2) Tool life comparison between semi-continuous surface and discontinuous surface. The cutting test of the top surface of the cylinder head was carried out twice. The tool life was 200 and 242 workpieces respectively. The main failure mode was blade chipping, in which the edge of the wiper edge was 100% and the edge of the cutting edge was 83%.
A total of 8 tests were carried out on the bottom test of the cylinder head. The average life of the tool was 424.5 workpieces. The main failure mode was blade chipping, in which the wiper edge rate was 25% and the cutting edge chipping rate was 29%.
It can be seen from the above test that for intermittent surfaces such as the top surface of the cylinder head, the cutting impact has a great influence on the PCBN blade, and the PCBN blade chipping rate is too high, which is obviously not suitable for the application of the PCBN blade; The semi-continuous surface, the impact of the cutting impact on the PCBN blade is still very large, the PCBN blade chipping rate is much lower than the intermittent surface of the cylinder head top surface, but the relative carbide blade is also higher, the PCBN blade has a certain Application prospects.
(3) Failure mode of the PCBN blade. The main failure mode of the PCBN insert during the test is blade chipping (see Figure 6 and Figure 7). A small amount is the wear of the cutting edge and the compression of the compression point after the abnormal compression of the body. The failure mode is mainly caused by blade chipping. We believe that there are mainly the following aspects: (1) The cutting edge is chipped during the cutting process due to the impact of intermittent cutting. 2 After the cutting edge wears, the cutting force increases to cause chipping. 3 The cutting edge encounters residual cutting fluid during the cutting process, causing chipping due to thermal shock. 4 After the cutting edge wears, the cutting force increases, causing the cutter body to be crushed. After the blade is chipped, the cutting force continues to increase, causing the blade body to be crushed. 6 The cutting edge has insufficient brazing strength and cannot withstand the impact, causing the cutting edge to chip.
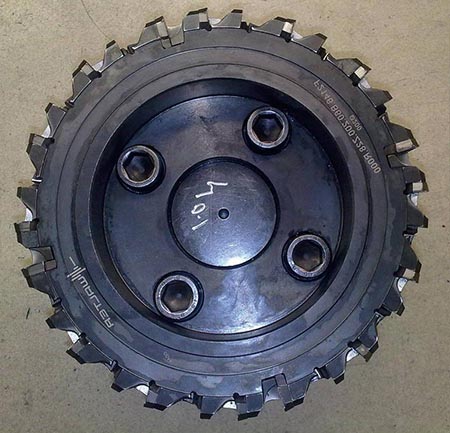
Figure 6: PCBN semi-finishing milling cutter processes the damage of the blade after the bottom of 400 cylinder heads
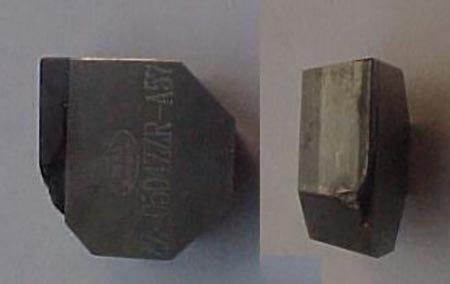
(a) The wiper blade is chipped
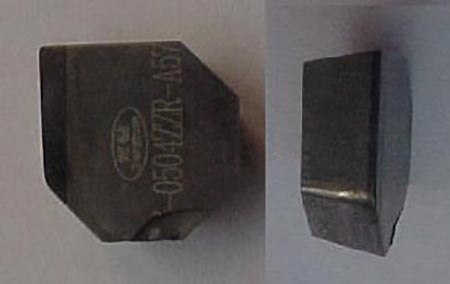
(b) Wear of the wiper and cracking of the pinch point
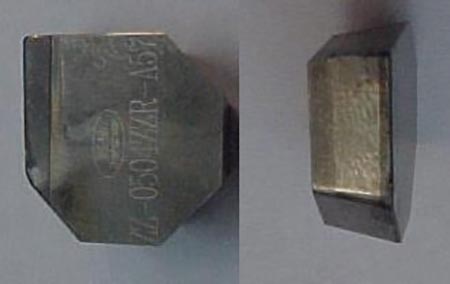
(c) wiper wear
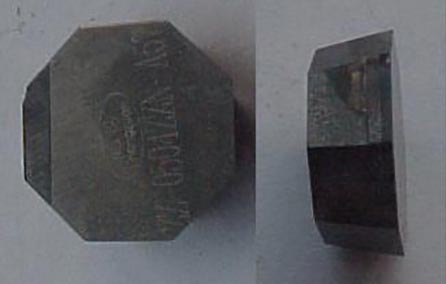
(d) Cutting edge wear
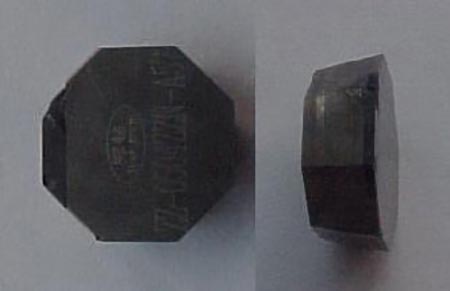
(e) Cutting edge chipping
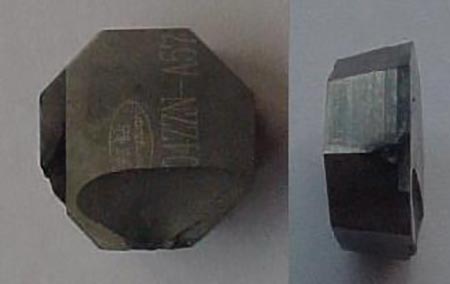
(f) Cutting edge chipping and pinch point cracking
Figure 7 Failure mode of PCBN blade
(4) The relationship between spindle power and blade wear. Figure 8 shows the relationship between cutter life and power tracked in one test. The life of the cutterhead is from the beginning of machining to the processing of the 150th workpiece. The spindle power is relatively stable. From 150 to 200 workpieces, the spindle power starts to increase, indicating that the blade wear is increased. Between 200 and 250 workpieces, the spindle power increases rapidly. When machining to the 233th piece, one cutting edge is chipped, and two cutting edges are slightly blasted; between 250 and 400 workpieces, the chipping continues to increase, but the spindle power tends to be stable due to the blade cutting after chipping. The blade is equivalent to the state of the new blade. When machining to the 411th workpiece, the blade fails and the surface quality deteriorates. After the removal, it was found that there were piled tumors on the surface of the wiper blade, 6 blades of the cutting edge were cracked, and 8 blades exploded.
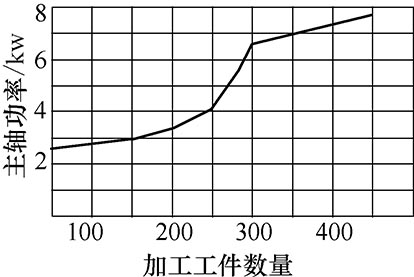
Figure 8 Relationship between spindle power and blade wear
(5) The relationship between cutting fluid and blade life. When the PCBN tool is applied to the bottom surface of the cylinder head for semi-finishing, the average life of the cutter head is only 917 holes, and the 100% life expectancy of the tool is only 32%. After on-site analysis, it was found that since the cylinder head width is larger than the milling cutter diameter, when milling the bottom surface of the cylinder head, the horizontal and vertical passes are divided. The CNC program sets the horizontal pass of the upper half and then the lateral pass of the lower half (see Figure 9). During the upper half of the transverse pass, the residual liquid in the cooling water pipe beside the machine spindle is splashed onto the lower half of the bottom surface of the cylinder head (see Figure 10). Therefore, when the PCBN insert grinds the lower half of the bottom surface of the cylinder head When the high temperature PCBN blade encounters the cutting fluid, it cracks. Improvement measures: Modify the CNC program, first mill the lower part of the bottom surface of the cylinder head (see Figure 9). After the improvement, the average life of the cutter head rises to 1 113 holes, and the 100% life of the tool reaches 93% (see Table 1).
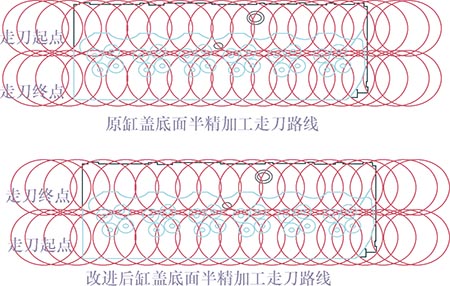
Figure 9 PCBN milling cutter path before and after improvement
Figure 10: The cutting fluid residue splashed on the bottom of the cylinder head causing chipping
It can be seen that the PCBN blade is allergic to the cutting fluid of the machine during use, and the supply of the cutting fluid should be cut off during the processing.
(6) Tool cost. According to the test conditions, the semi-finishing of the bottom surface of the cylinder head was tested. In the test, 4 sets of cutting edge inserts (48 pieces in total) and 5 sets of polishing edge inserts (20 pieces in total) were used for 8 tests, and a total of 3 396 workpieces were processed. , the quality of the workpiece is qualified; PCBN semi-finishing single piece time is 40s, compared with the carbide blade, reducing the beat for 20s.
The cutting edge test averaged 424.5 pieces per cutting edge, each blade can be indexed once, with an average life of 849 pieces per piece; the wiper blade averaged 679 pieces (not indexable). Each blade costs 235 yuan, so the cost of a single blade is 4.7 yuan, the cost is 1.2 yuan higher than the carbide blade.
2. Application tracking
Before the completion of the expansion test PCBN blade is ready for use, it is necessary to first establish the operating standard, as specified below:
(1) The cutting edge of the first cutting edge of the first cutting edge does not exceed 1/3, and can be used for indexing.
(2) According to the test result, the machine tool monitoring life of the milling cutter is set to 1 200 hole surface (the actual number of workpieces to be machined = the monitoring life ÷ conversion coefficient, the conversion coefficient of the tool is equal to 3).
(3) After the first installation of the wiper blade, follow the cutting edge to the cutting edge life (400 workpieces, machine tool life of 1 200), if there is no chipping and the amount of wear is small, allow the second use .
In 2009, the tool life of the semi-finishing process of the cylinder head production line was continuously tracked for 3 months. Table 2 shows the actual use of the CBN milling cutter. It can be seen from Table 2 that the average index of the cutting edge is 0.6 times, which is far from the one in the test stage; the wiper blade can only be used once on average, and there is a certain gap between the two parts in the test stage; The cost of the tool is 7.02 yuan, which is also far from the calculation cost of the test phase. However, due to the 10% reduction in the tempo of the CBN tool, the production capacity has been improved.
references:
[1] Fu Zhifang, Liu Yuehua. Analysis of Tool Technology in High Speed ​​Cutting[J]. Modern Corporate Culture, 2010(21): 157.
Led Outdoor Lightings
Our LED outdoor lightings range of LED ground lights are a great lighting solution to the in-ground illumination of your outdoor spaces. Using the latest in LED technology they are a low energy - low maintenance - long life.
Features of these led outdoor lightings are:
1.Stunning designs,the fascinating designs, highly waterproof IP65-IP68, quality and price
2.Compare us with the best outdoor lighting manufacturer before buying the products
3.Free installation guide is provided with each product
4.High quality architectural LED Outdoor Landscape Light at economical prices & 3 years warranty
Various outdoor lightings,Durable outdoor lightings,Dimmable outdoor lightings
SHENGYA LIGHTING TECHNOLOGY CO., LTD. , https://www.syalighting.com