Plastic products will emit an unpleasant smell during processing. The bags or some plastic products will have some thick plastic flavor. The reason for this problem is the problems in the production process. This article provides you with seven solutions:
There are four main reasons for odor after granulation. The first is that the material is more complicated, the second is the material is processed and degraded many times, the third is the decomposition of small molecular materials in the material, and the fourth is the water and some materials play a very good role. Strong accelerated degradation.
1, the correct use of additives
The tertiary amines used in the production of polyurethane foams often give rise to strong odors and fog on the interior windows of automobiles. The solution to this problem is to find alternatives to these amines. If a polyhydroxy compound is used, the polyhydroxy compound is not only a component of the polyurethane molecular chain, but also has catalytic activity.
Phenol stabilizers used in PVC extrusion or calendering processes are also often replaced by low odor zinc stabilizers. The heat stabilizer tin octylate is also commonly used in automotive PVC products due to its low odor and low atomization properties. Plant extract oils such as erucic acid and oleic acid are much less odorous than amine lubricants (for polyolefin and styrenic food packaging materials) made from animal extract oils.
2. Processing of recycled materials
The organic solvent extraction method helps to remove odor-causing compounds. The latest solvent extraction method also uses supercritical carbon dioxide as a solvent. This technology has been applied to HDPE and PET to remove odorous contaminants from oil containers, pesticide containers and other waste devices. The benefit of carbon dioxide extracts is that they do not cause troublesome post-treatment problems with organic solvents.
The odour removal unit is an integral part of the waste plastic pellet extruder and is also effective in removing some of the highly volatile compounds that produce odors.
3, using a more pure resin
In many plastics, especially in plastics such as polyvinyl chloride, styrene, polyethyl acetate and acrylates, residual traces of monomers can produce unpleasant odors. Those odors can be eliminated by using a resin with a small amount of monomer remaining.
4, adding adsorbent
If a small amount of zeolite (an aluminosilicate adsorbent) is filled in the polymer, the effect of removing the odor of the material can be achieved. Zeolites have a large number of crystalline voids that capture small molecules of odorous gases.
Molecular adsorbents have been successfully applied to polyolefin extruded tubing, injection and extrusion blow molded containers, insulation packaging materials, extruded outer packaging materials and sealing polymers. Molecularly adsorbed powders can also be added to plastics as moisture absorbers to remove moisture, which can also contribute to the odor of plastic products.
5, the use of antibacterial agents
Adding an antibacterial agent to the plastic not only reduces the odor it emits, but also delays the aging, discoloration and embrittlement of the surface of the product. The most commonly used antibacterial agents are 10,10'-oxobiphenanthrene, trioxyhydroxydiphenyl ether, isothiazolinone, pyrithione. Organometallic compounds containing tin and silver are sometimes also used as antibacterial agents.
6, using the desorption method
Another method of deodorization is to place the plastic in an odor sorbent such as activated carbon and high surface area silicate. The vacuum treatment environment can accelerate the desorption process. Treatment of plastic particles with a special detergent solution can also help to remove odors. Generally, these cleaners are aqueous or alkaline solutions containing surfactants. These detergents can effectively remove vinyl chloride monomers, styrene, acrylates, acrylic monomers, and unsaturated hydrocarbons.
7, add fragrance
Adding a fragrance to a plastic does not actually eliminate the unpleasant odor, but it can cover these odors a lot, and in many cases this is enough. The method can be applied to polyethylene, polypropylene and polyolefin thermoplastic elastomers by injection molding, extrusion or blow molding.
The fragrance retention time is not equivalent to the life of the molded part. Its retention time depends on its degree of aggregation, volume to surface area ratio, exposure to heat or moisture, and whether the molded part will be rigorous. Insulate air packaging and many other factors. Fragrances are generally used in toys, household goods, cosmetic containers and household appliances.
Steel Wire Rope
Brass Plated Steel Wire Rope,Galvanized Steel Wire Rope and Stainless Steel Wire Rope is the basic material of Diamond Wire Saw. The Wire saw is an advanced engineering tool used in the renovation and reinforcement of construction factories. It is a special cutting tool, suitable for cutting hard materials such as reinforced concrete, rock, ceramics, brick walls, etc. The specifications of the wire saw are mainly controlled by beading. The formula of different stones is different. The production of beads should be customized according to the actual situation of the stone to maximize the efficiency. With the continuous research and development and technology accumulation of various production units in my country, the formulation process and manufacturing of domestic diamonds have reached the international leading level.

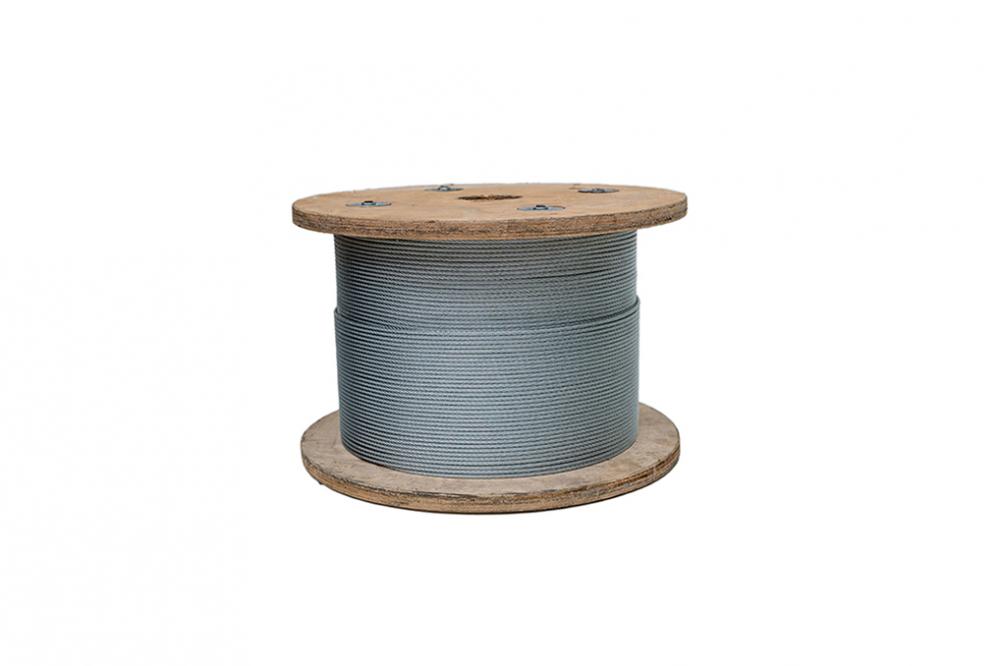
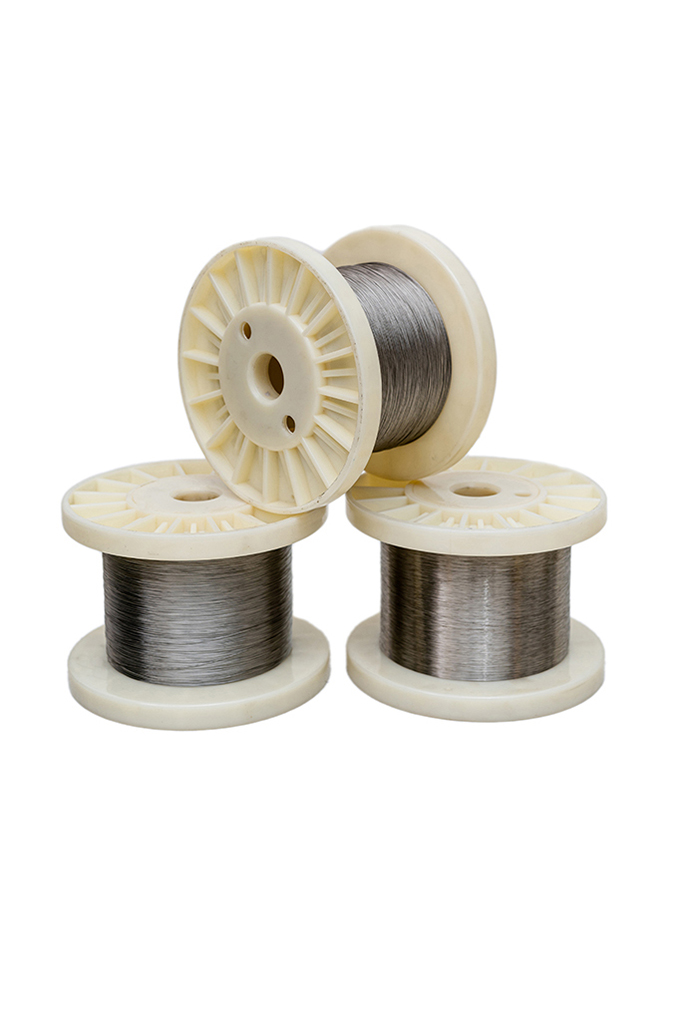
Wire Rope,Galvanized Wire Rope,Coated Wire Rope,High Strength Wire Cord
Jiangyin Baoneng Precision New Material Co.,LTD , https://www.baonengwire.com