The automotive transmission is a major component of the automotive powertrain transmission system, and its performance and life are directly related to the quality of the vehicle. With the increasingly strict restrictions on vehicle noise in national regulations and the increasing demand for ride comfort by car buyers, the control of vibration and noise in domestic transmissions is urgent. The car transmission is a complex transmission system consisting of gears, shafts, bearings, housings, shift forks, fork shafts and synchronizers. During the rotation of the transmission, not only the noise related to the shaft frequency is generated, but also the noise related to the meshing frequency of the gear, and the natural frequency of some components, so the collected noise signal is actually the above noise. Superimposed. If the signal is simply analyzed by the power spectrum, it is difficult to find the noise source.
According to the feedback of a self-owned brand manual transmission (SC30M5C) of the self-owned brand of Shanghai Auto Passenger Vehicle Company, the third-speed taxiing whistle problem (speed 1400~2400r/min) lists the possible factors and conducts vibration and noise tests one by one to identify the main ones. Noise source. After the preliminary study on the mechanism of vibration and noise generation in the gearbox system, the transmission-related parts were optimized and matched, so that the howling was improved.
status quo
The project team of our factory detected the 13th and 20th order vibration noise problems of the NVH (noise, vibration and sound vibration roughness) of a self-owned brand model of the SC30M5C transmission. The vibration noise meter sensor arrangement is shown in Figure 1.
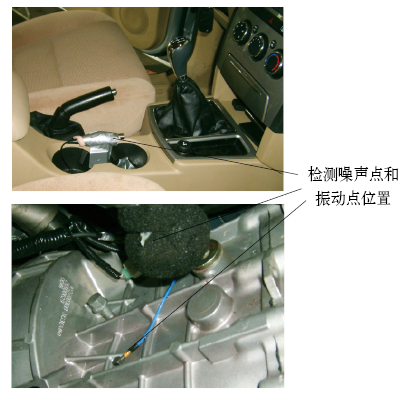
Figure 1 Vibration noise meter sensor arrangement
The F80# test sample car has the noise of “呜呜†howling, and the data measurement results are as follows:
1) 1, 2, 3, 4 speed acceleration and reverse drag and slide normal.
2) 3 stop acceleration, full throttle acceleration is no problem; after acceleration to 3000r/min, there is noise when dragging. When the speed is 2400r/min, 13th-order meshing noise appears first, then 20th-order superimposed noise appears until the speed is 1400r/min. The noise disappears, and the noise is maximum when the speed is 2000r/min.
3) In the anti-drag spectrum diagram (see Fig. 2), there is a bright band in each of the 13th order and the 20th order of the third-speed sliding. The subjective evaluation has obvious howling.
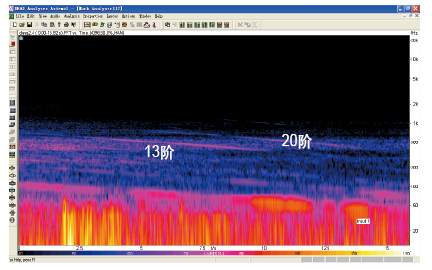
Figure 2 Spectral map with subjective evaluation with obvious howling
For the howling problem, the untransmission transmission is tested. The results are shown in the attached table. The details are as follows.
In good condition
The existing gears of five sets of transmission gears are sampled (one-axis + three-speed, intermediate-shaft gears), and the results meet the technical requirements; the F23# transmission is dismantled and tested, and the one-axis + three-speed transmission of the 28# transmission is tested. Technical requirements, in good condition.
2. Slightly whistling
1) Conduct a driving evaluation of the B90# sample car together with the user, confirming that the transmission has a slight howling and the state is good.
2) Replace the F23# transmission (drag torque 1.0N·m) to the B90# car for driving evaluation. When the 2nd and 3rd gears are decelerated to 2000~1500r/min, the transmission will be howling. The F23# transmission drag torque was re-adjusted to 1.9 N·m, the loading and driving evaluation, the howling was improved (very slight), acceptable.
3) Extract two sets of qualified gears, 39#, 40# transmission case packing, loading and driving evaluation, whistling slightly, good condition.
4) After the 28# transmission and the 39# transmission's one-axis and three-speed gears are swapped, the 28# transmission whistle is very slight, the state is better, and the 39# transmission whistle is also improved (slightly) and acceptable.
5) Assembling the 41# transmission, 0925# transmission and 42# transmission with three tooth marks, the loading and driving evaluation, the howling is improved (very slight), acceptable.
3. Obvious whistling
Randomly take inventory 28# transmission, drag torque is 1.5N·m, loading and driving evaluation, 2, 3 gear deceleration to 2000~1500r/min, the transmission has obvious howling, unacceptable; re-adjust the towing torque to 1.9N · m, howling does not improve.
The transmissions with howling and very slight howling faults are detected on the calibration gantry and cannot be distinguished. The NVH measurement with the instrument results in a 13th-order bright spot, which is different from the 20-order vibration of the vehicle state, which may be caused by the vibration of the test bench. Therefore, the howling failure cannot be discerned on the calibration station. Through the vehicle NVH measurement, it is determined that the howling is 20 orders.
Analysis of the cause of howling
1. General principles of howling diagnosis and analysis
First of all, do not easily remove the car transmission from the vehicle, and then find the cause of noise and sound failure. Because the noise abnormality of the automobile transmission is related to the mechanical parts of the engine, the transmission shaft and the transmission, there are many possible causes and locations of noise anomalies and audible faults, and the exclusion method is often used to find the comparison benchmarks. Therefore, the transmission should be installed on the whole vehicle, and the NVH tester and sensor should be arranged for testing to determine the approximate location and cause of the fault.
2. Order tracking and order spectrum analysis
Although the corresponding software conditions are not yet available, based on the information from the customer feedback and the results of the vehicle test, the spectrum analysis is initially performed on the collected data, and three characteristic orders of 13, 17.5 and 20 are obtained, of which 20 orders are used. The noise contribution is the largest.
3. Transmission structure analysis
The gear, shaft and bearing parts of the SC30M5B transmission are shown in Figure 3. In the entire drive train, the drive consists of the part and the remaining five bearings (the transmission has two short cylindrical roller bearings and five tapered roller bearings). . Among them, the number of teeth of the four gears 1, 3, 5, and 6 is 20, 27, 29, and 33, respectively. The number of rolling elements of a shaft outer diameter tapered roller bearing and one shaft inner bore small tapered roller bearing are 14 and 13, respectively, and the number of rolling elements of the intermediate shaft front end and the middle tapered roller bearing are both 17, and the intermediate shaft rear end short cylindrical roller The number of rolling elements of the sub-bearings is 12, and the number of rolling elements of the two-axis central tapered roller bearing and the two-shaft rear deep groove ball bearing are 14 and 12, respectively.
According to the order tracking theorem, the rotation frequency of the input shaft (one axis) is 1 step, and the relevant characteristic order can be obtained from the number of teeth of each gear of Fig. 3 and the parameters of each bearing. The gearing frequency of the three-gear gear pair is 20 orders, the rotation frequency of one-axis bearing is 14 and 13 orders, the rotation frequency of the two-axis bearing is 9.1 and 7.8 orders, and the rotation frequency of the intermediate shaft bearing is 10.3 and 7.3. Secondly, the comprehensive test data analysis and structural analysis show that the main noise source of the transmission whistle is the assembly fit of the one-axis and two-axis tapered bearings and the meshing precision of the third gear pair.
The specific reasons are as follows:
1) According to the NVH measurement of the whole vehicle, it is determined that the howling is 20 and 17.5 orders (mainly the 20th order causes howling), which corresponds to the transmission as a shaft gear of 20 orders and 17.5 orders. The current one-axis measurement results meet the specifications.
2) Improve the accuracy of the one-axis gear, and the howling will be improved. However, due to structural constraints, the one-axis gear can only be shaved and cannot be honed.
3) The meshing spots of the gear have an effect on howling.
4) The drag torque has an effect on the whistle of some transmissions, but the drag torque cannot be too large due to the adjustment requirements of the tapered bearings.
improvement measures
The third gear of the intermediate shaft adopts the honing process to improve the tooth surface smoothness. As with the current meshing process, the honing test can be performed. Continue to carry out the vehicle driving evaluation (NVH test) for the key components involved (one-axis assembly, three-gear gear assembly, intermediate shaft) to further determine the possible causes of howling. The two transmission assemblies (one howling, one without howling) do the engagement spot test of the tooth faces of the various gears. The pre-tightening torque of the current assembly is tracked and debugged, and the tracked transmission is evaluated for loading (NVH test).
After the howling is improved (slightly whistling), there are only weak highlights in the anti-drag spectrum, and there is no problem in subjective evaluation (see Figure 4).
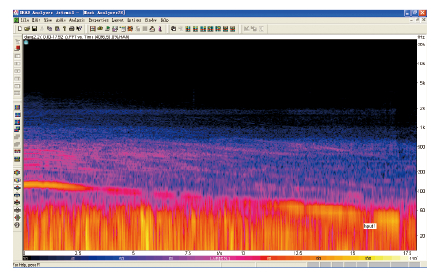
Figure 4 Spectral diagram of subjective evaluation of slight whistling
The specific measures are as follows:
1) Tooth-engage the countershaft gear and select 110 sets of toothed intermediate shaft assembly. The intermediate shaft gears were meshed with the teeth, and 20 sets of toothed intermediate shafts were selected, and 20 sets of transmissions were assembled in strict accordance with the requirements of the assembly work instructions. And 10 sets of transmissions are equipped with record data, one-to-one correspondence with the transmission for subsequent tracking.
2) Appropriately reduce the assembly interference of one-axis and two-axis tapered bearings with one-axis and two-axis.
3) The intermediate shaft third gear adopts the honing process to improve the tooth surface finish.
The transmission products assembled after taking the above measures have received satisfactory feedback from users.
Conclusion
Howling has become a common type of NVH in vehicle development. In the product development stage, it is necessary to carry out vibration and noise test and analysis instruments for monitoring on the whole vehicle, with manual monitoring to identify and improve the identified howling. After the transmission is put into production, our company can install the new version of Discom-Noise Analysis Systems test analyzer with the whistle-clearing function on the transmission assembly checker, which can basically identify the whistling products and realize good online detection and process. control.
High Speed Door
High speed shutter door is a rapid operating, anti-crash shutter door for indoor application . The most advantage of this door is that the opening/closing speed can reach to 0.6-1.8m/s, really fast action a lot than tranditional rollling shutter door. short opening and closing times reduce cooling loss, avoid airflow and enable a smooth operating procedure. They can also be designed in larger dimensions for the mining and aircraft industries.
High speed door can be easily installed, economical,quiet and efficient with electromechanical drive.
This door quickly though in/out open gate, ideal for warehouses,factories, hangars use, widths can be from 2m to 20 meters.
The material of this door are variety: PVC curtain to keep the insdie clean, heavy duty aluminum door with wind-resisitant function can wrok in heavy windy weather, and also the freezer door can be used in cold warehouse or somewhere like that.
Including models are:PVC High Speed Door, Aluminum Spiral High Speed Door, Self-Recovery repair door, Cold Storage Room Fast Door.
High Speed Door,PVC High Speed Door,Aluminum High Speed Door,Spiral High Speed Door
Shenzhen Hongfa Automatic Door Co., Ltd. , https://www.hffastdoor.com